MISUMI E-XYZPG series crossed roller guide type positioning stages are economy series positioning stages. It can be used as a positioning stage for simple position adjustment. The body is made of aluminum alloy to achieve light weight; the surface is black anodized. Crossed roller guide is used for guiding, which can meet the required operating accuracy. Prices have been significantly reduced due to local production in China and improved machining process.
Feature 1: Production cycle is shortened, shipped within 5 days at the earliest
Feature 2: Low price is achieved by simplifying the structure and improving the machining process.
Feature 3: A wide range of alterations are available to enable installation and operation under different conditions.
Feature 4: By improving the clamping mechanism, the holding force of the positioning stage is greater than that of the standard type clamping mechanism.
Specifications Overview
E-XYZPG | Aluminum Alloy | Black Anodized | ±6.5~±12.5 | 9.8~49 | Within 10μm |
■Amount of travel The catalog drawing size is the state of travel 0mm, and taking this as reference, the distance moved in the left and right directions is the amount of travel.
■Load capacity is the force in N that the positioning stage can withstand when the center of gravity of the workpiece is in the center of the positioning stage. If used in excess of the load capacity, the positioning stage may not move properly or get stuck. Refer to the values of "Horizontal" and "Vertical" for the load resistance for horizontal and vertical installation respectively. Note that when the linear motion positioning stage is installed vertically or upside down, the accuracy may be less than the value indicated in the catalog.
■Straightness The maximum offset relative to the ideal axis of movement (the line connecting the start and end points is shown as the red line in the figure below. The black line is the actual trajectory of movement.) when the positioning stage moves at full stroke. Detection method: Place the micrometer on the positioning stage, with the pointer held against the reference block, let the positioning stage move at full stroke, and measure its maximum displacement, which is the straightness.
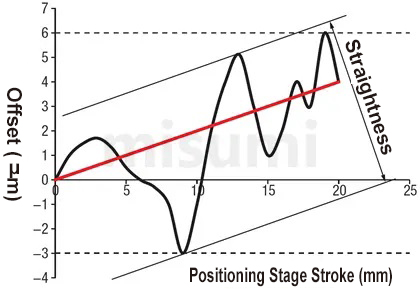

Usage Method
■Installation Method of X-Axis Positioning Stage When mounting the positioning stage to the base, basically it is mounted by moving the positioning stage surface. Refer to the following diagram.
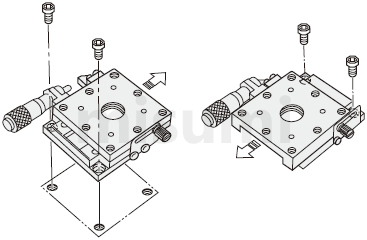

The above diagram is for demonstration purpose only. Refer to each catalog or 3D data for detailed shapes and specifications of the positioning stage.
■Mounting Posture | | 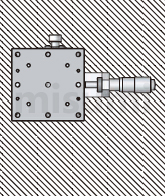 |  |
Horizontal | Inverted | Side-Mounted Horizontal | Side-Mounted Vertical |
○ | ○ | △ | △ |

Horizontal, inverted, side-mounted horizontal or side-mounted vertical installation options are available. Other installation methods should be given more attention.

Load capacity and accuracy will change greatly depending on the mounting posture.

○:Same as horizontal load capacity.

△:About 1/3 of the horizontal load capacity is the approximate standard, if the catalog contains the vertical load capacity, it should be given priority.
■Vertical Use of X-Axis Positioning Stage When using the X-axis positioning stage vertically, pay attention to the feed direction, which should not be in the same direction as gravity.
When using a micrometer knob type positioning stage, note that the positioning stage is reset by extension spring. If the force applied is greater than the spring load, the positioning stage surface may fall. For such occasions, alterations can be used as a solution.
|
(Usually) If the force applied exceeds the tensile load of the spring, the positioning stage surface may slip off because it cannot support the weight. | After selecting the alteration of the micrometer knob position change, the positioning stage surface does not fall even when used vertically. |
 |  |

Avoid applying loads that exceed the load carrying range in the vertical direction.
Example of Use
Mechanism name: Cotton swab glue application position adjustment

Example of Use
Electronics/Home Appliance | | Automotive | | Medical |
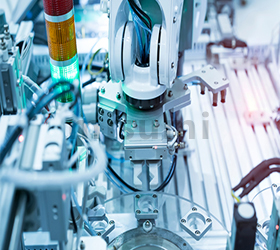 | |  | | 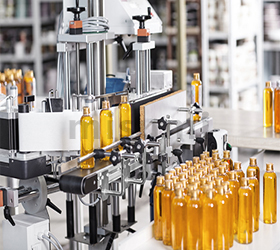 |
Smart Phones | | Semiconductor | | Lithium battery |
 | | 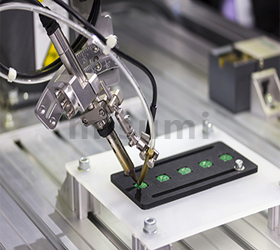 | |  |
Precautions
■Operating temperature and environment
Recommended operating environment: 10~50℃, 20~70%RH (no condensation)
Accuracy assurance environment: 22±5℃, 20~70%RH (no condensation)
■Guiding mechanism
This positioning stage adopts crossed roller guide as the guiding mechanism. Please refill the lubricant at the right time according to the usage conditions to prevent the life of crossed roller guide from being shortened due to the decrease of lubricant and aging.
■Clamping mechanism
①The clamping mechanism of the positioning stage is fixed by the frictional force generated by the fastening screw, so when the applied external force exceeds the frictional force of the clamping mechanism section, it will cause the positioning stage to move. The user should take appropriate measures to avoid movement of the positioning stage surface during use. If clamping reinforcement is required, disc clamping or opposite clamping can be selected.
②The holding force is the value of the force that keeps the positioning stage surface from moving in the clamped condition. Since the maximum holding force varies with the tightening torque, please ensure a sufficiently large safety factor when designing.
■Feed mechanism
The shape of a positioning stage with a micrometer knob installed as shown in the figure below is generally called the standard type. Free selection is possible by combining the installation space, mounting posture, and operation method. However, due to the structure of the product, there are some models where the installation position of the micrometer knob cannot be changed. For details, refer to the [Alteration] at the bottom of each product page.

■Flatness of the mounting surface
The upper and lower positioning stage surface may be deformed due to the different flatness of its mounting surface. Deformation of the positioning stage surface may result in gaps, looseness due to failure to obtain the specified preload, or poor sliding due to excessive preload. Therefore, it is recommended that the flatness of the mounting surface be kept at about 5 microns.
Related Products
How can we improve?
How can we improve?
Thank you for your time.
Your feedback is essential for our continuous improvement
Privacy Policy
Thank you for your cooperation.
Thank you for your time.
Your feedback is essential for our continuous improvement
Please use the inquiry form.
Privacy Policy